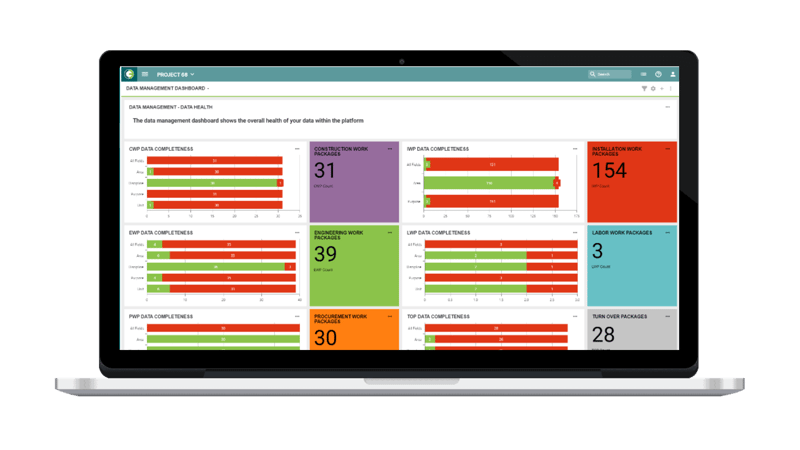
O3’s partner Insight AWP is in the business of implementing work packaging in the field and depends on good quality software to manage the process. Which ultimately relies on good quality data. Insight helps project teams define the data requirements needed to support a healthy Advanced Work Packaging program while O3 leverages the well-organized data to populate our work packaging software and drive users to act.
Data Challenges
Some challenges associated with AWP include getting the correct data to begin with. Data requirements should be established in the contracts. Getting data in the correct format is important for standardization, by using templates and an attribute table this can be corrected. Over, shorts and Damage can be a challenge for data delivered to a common portal, screened and accepted or rejected. Storing data in a “warehouse” can be a challenge where it can be sorted by key attributes by tag number or construction work package. Access to data is a very common issue because the need for the right person with the right access to a secure platform must be used. Using the data in and of itself can be a challenge. That’s why O3 is the “truth serum” to show you the gaps in your data. Meaningful reports can be a challenge if you’re not using the best software because you need one source of truth for accurate reports.
Data Solutions
AWP Insight builds a matrix of attributes that starts with data consumers including Material Management, Construction, Quality Assurance, Turnover and Operations. Once consumers have established Insight then figures out what each of them needs. From there they back up to the 3D model and engineering to find out what they typically publish and in what format. This gap between these points is the action list.
By using a centralized data warehouse data is collected into a single common pool from all projects. A “gatekeeper” screens the data as it arrives and then facilitates quality control. The project cloud provides secure, easy, on-demand access for all project stakeholders. Data also feeds project reports and dashboards.
Good quality data and software that organizes it make all the difference on a project. It allows WorkFace Planners to identify the work front that can be executed, which creates the benefit from all of this effort. Ultimately, you’ll be supercharging your construction productivity.
How O3 Uses Data to Support AWP
As a software provider, we have witnessed firsthand the benefits of having a data strategy in place to support AWP.
First, there’s accessibility. When data is managed in multiple sources, there may be issues with people not having access to an application or file. Maybe the engineering team has the status of documents stored in an excel sheet that no one outside of the engineering team has access to. Or a planner needs the know if a material is available for a work package but doesn’t have access to the material management software. Since O3 is a cloud-based application and there is no limit on the number of users, this data can be available at any time without relying on anyone else to provide it.
A second benefit is one that often isn’t known until data is in O3 – and that is data accuracy. When data is all visible in one platform, it will be compared across ALL sources which makes any inaccuracies or inconsistencies become obvious. By having that data in O3, these inconsistencies, such as differences in nomenclatures or dates not lining up, will be highlighted. And discovering the gaps in the data is a good thing – it’s best to find that early on.
The third benefit is creating automation and reporting based on relationships between data from different sources. A single system may show you a list of documents or drawings that are associated with a work package, but O3 will go a step further and provide notifications based on data currently available – if a document is not complete and the planned start date of a Work Package is only a few weeks away. O3 offers this and many other types of relationships that can be used to create and clear constraints automatically all without any changes to the current process.
The Client Success Team works with each project or facility to understand the type of data sources needed to support where you are in your AWP journey. If you are still relatively new to AWP, you may only want to connect a few sources, such as a materials management system, your P6 schedule, and a couple of Excel spreadsheets.
But as your AWP program matures, O3 can work with you to support a holistic data management strategy. Geoff talked earlier about how he has helped projects set up a project cloud and a data warehouse. We can also work with an existing data lake or structure that your organization may already have in place.
Data can be consumed in O3 in a variety of ways:
- Our proprietary API
- Webhooks
- Flat file imports,
- Or a combination of these
Our advice (similar to the process of AWP) is to begin with the end in mind – and implement a “crawl, walk, run” plan for your data strategy. Start off with imports of the data using the existing format to understand the data you already have. Then set expectations for exchange – fields format and frequency, and establish reporting to track the data health and accuracy. Move to semi-automated and API-level integrations as your comfort level increases. Having RESTFul APIs and webhooks allows administrators to interface and connect more easily during the Run phase. We’ve got the experience and battle scars to give you recommendations and guidance along your journey. We’ve seen it all as we’ve worked with our global clients and different project sizes and types.
As an example, we discovered some international companies use semicolons to separate data instead of commas in CSV files. O3 was easily configured to support this particular use case, as well as commas, semicolons, and any other separators. If you’ve got the data, we can meet you where you are!
O3 has a default data management dashboard to help you visualize how data is flowing into the platform. The dashboard is configured to know what systems are being used on the project and what data is required from those systems ( with fields, format, frequency). O3 automatically raises a flag when the necessary data is not received, helps Information managers know which areas to focus on, and then he or she can assign follow-up action items to resolve any issues.
The result of all these data connections is work packages that are ready to go. It’s not about getting O3 populated to show you pretty dashboards. It’s about giving you an easy-to-understand visual representation of your data so you can make decisions faster, with up-to-date information.
This is an example of how O3 uses this data to show you if a package is ready to be released to the field. The items in green are ready, the items in yellow are still waiting for issues to be resolved – such as a drawing that still needs to be finalized or a material that has not yet arrived, and the items in red are critical. A package may need to be released in the next 2 weeks, but we still don’t have a material onsite. You can click into that red item, get details about what’s holding up the work and assign a task directly to a person with a due date and priority to make sure that the package can be released on time.
This view can be used by an Owner / Project Manager / Contractor / Supplier or ANYONE who owns a constraint on the project. With O3’s unlimited user model, you can provide guest access to any company or team so they can provide updates as needed. With configurable roles & permissions, you can ensure that each role or company can only see the information that pertains to them.
O3 can use data connections to highlight in a 3D model packages that are available for release and packages that are still waiting to be cleared. Showing this directly in a model can help you see specific work areas and the available work packages in that area to help you plan your work accordingly. You can also slice and dice the data by work area, work package type, discipline, or component type.
You can zoom in to any area and click to see component or work package details. Again, all of this information helps you take action right away. See a work package you want to include in your plan, but it’s still constrained? You can drill down to that IWP and assign the constraint or leave a comment directly in the system that will notify the owner that they have an action item to address. As the constraints are cleared, you will be notified via email and the status in the model will update to let you know that you are good to go.
Finally with role-specific dashboards, making critical decisions has never been easier – or more data-driven. Contractors can see their specific scope of the project and track their progress, Construction Managers and Project Managers can see the overall health of the project – if they are on schedule, if AWP best practices are being followed, and how each team is performing.
The leadership team can see high-level reporting in a red-yellow-green stoplight view so they can focus only on the areas that need their attention and not leaf through hundred-page reports with a fine-tooth comb and attempt to identify problems. Cross-project reporting is also available so Owners or EPC firms can see at a glance how each project is progressing in their portfolio.
Key Takeaways
First, Standardizing data is a critical step in your AWP journey. Software is a “truth serum” for data. Once you can visualize the information, you can more easily identify problem areas. And the earlier you know about them, the better. It is never too early to start your data strategy. Even if you only get started with connections on one or two systems, it makes a huge difference in your program. Having one view of all AWP data provides many benefits including resolving access & accuracy issues and identifies any roadblocks based on package relationships. Automation reduces errors and helps you take action quicker. Let technology and automation do the heavy lifting and focus your energy instead on making decisions and taking action. Most importantly, make decisions based on data, not hunches. Standardizing the way work packages are created, progress is reported, and updates are tracked will help increase productivity, reduce costs, and improve the quality and safety of your work.