“We have a project kicking off next week and we would like to implement Advanced Work Packaging. Can you help?”
I hear this a lot, and of course in most cases the answer is yes. But the key to the question is in understanding what is meant by “kicking off”?
If you mean that the project is starting the early Front End Loading stages (Assess, Select, or even Define), we can help a lot. If, however, you mean that foundations have been poured, anchor bolts set, and you have large equipment or modules arriving next week, the answer changes somewhat.
Don’t get me wrong – there are still things we can do in that second scenario. But you need to clearly understand that much of the value of AWP has already slipped away.
Timing, as the saying goes, is everything. And as much as that is true for life in general, it is absolutely critical for AWP. The effectiveness of implementing AWP on a project diminishes over time, in much the same way that constructability does. If you start your constructability process at the 60% model review, much of what you identify will already be too late to correct. Similarly, if you build your AWP Path of Construction during the Execute stage or try to determine the optimal installation sequence once the construction contractor bids have been received and the workforce is mobilizing to site, you have lost a crucial opportunity to influence the project outcomes.
All too often, AWP is an afterthought on a project, or (even worse) a reaction to poor execution of initial disciplines and is used as an attempt to claw back bad performance. AWP is not AWP if you start it during the construction phase. This is called WorkFace Planning.
So, this begs the question: When should AWP be started? If you are following a standard capital project format, the best answer is immediately after concept select. And even this answer comes with the caveat that we are assuming that construction personnel have had input into the concept select process.
Once you know what your chosen project solution will be, and other options have been assessed and ruled out, your AWP process should kick off in earnest. By starting at this early point, you can begin to assess and align the many elements that make AWP successful, including:
- Create your Construction Work Areas (CWAs). Break your plot plan up into manageable and logical pieces.
- Create your first pass Path of Construction. Begin to identify Engineering, Procurement and Fabrication / Modularization constraints.
- Get the Engineering contractor thinking about their scope in the context of your CWA breakdown and the priorities identified in your path of construction.
- Break up the design quantities using the CWAs, so that your estimate can reflect the work packaging plan.
- Make sure your schedule reflects the path of construction, and adequately identifies logical interface points between Engineering, Procurement, Fabrication / Modularization and Construction.
Can you wait until FEED (FEL3/Define)? Sure, but the sooner the better. Waiting for the start of FEED won’t be a big impact, unless you are changing Engineering contractors. Starting AWP at the end of FEED, or past Final Invest Decision (Funding) will put unnecessary strain on the Detailed Design process, causing churn and delays just at the time that you want Engineering to be ramping up to full production.
Waiting until the beginning of construction? Well, you aren’t really doing AWP, but rather WorkFace Planning (WFP). For some contractors, where the Owner is not pursuing AWP during Engineering, this is an unfortunate reality. Some value can still be gained, but you are dealing with the age-old construction issue of drawings and materials turning up when they are ready, in whatever order they arrive, rather than a well thought out sequence that will work for construction.
The graph below represents an attempt to capture this understanding of diminishing impact based on the timing of when you start AWP. The message is clear; the earlier the better.
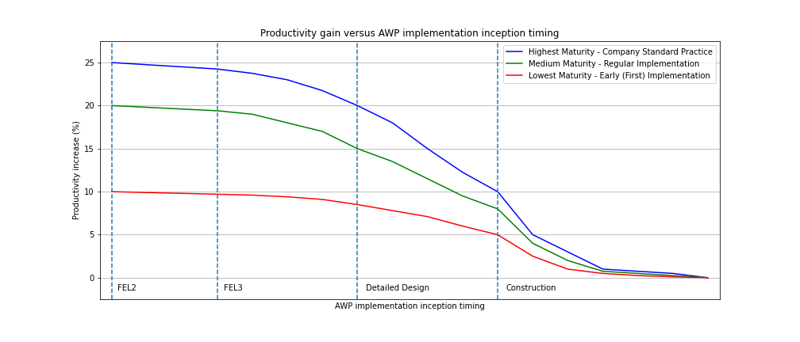
You can also see that there are three curves, representing the varying stages of AWP maturity within an organization or project team. But while the maturity will impact the overall productivity gain, the profile of each line shows the same effect for timing.
As I discussed in a previous blog, Owners Own AWP, and Owners will have the greatest influence over the timing of adoption. Unless the Owner is aware of the diminishing returns that the project will see across the phases, we will continue to see last-minute implementations and knee-jerk reactions to performance crises.
So whatever project you are working on, make your AWP plans early, and realize all the benefits that timely implementation can deliver.
For more information contact us today!