Managing data across multiple sources can help the AWP process in many ways. Data management is something that happens on all projects regardless of size or phase. It can range from data entry into different sources such as creating a work package matrix in Excel or compiling the full list of documents in a DMS. It could also be updating the schedule in P6 and sharing it with all stakeholders. O3 is focusing on data management that can be interfaced from all of these sources into one single application.
O3 is not changing the need to manage information across multiple sources because it’s not meant to be used as a material management system or document management system. Instead, O3 helps solve the common issues found when implementing data on several different projects.
Integration with O3 Is Easy
Some of the most common issues with data management on projects include accessibility, accurate data, data relationships, and integration management.
When data is managed in multiple sources there will always be an issue with people not having access to an application or file. Since O3 is a cloud-based application and has no limit on the number of users, data can be available at any time without relying on anyone else to provide it.
Data accuracy is a very common issue. When data is managed in one solution it can be compared across all sources which eliminate inaccuracies or inconsistencies.
Automation and reporting based on relationships between data from different sources can be a challenge. A DMS may show you a list of documents that are associated with a work package, but O3 goes a step further and notifies you if a document is incomplete or the start date is soon.
Data integration requires a lot of time and a strict set of rules when done manually. O3 offers a way to do this automatically and makes the process much more seamless.
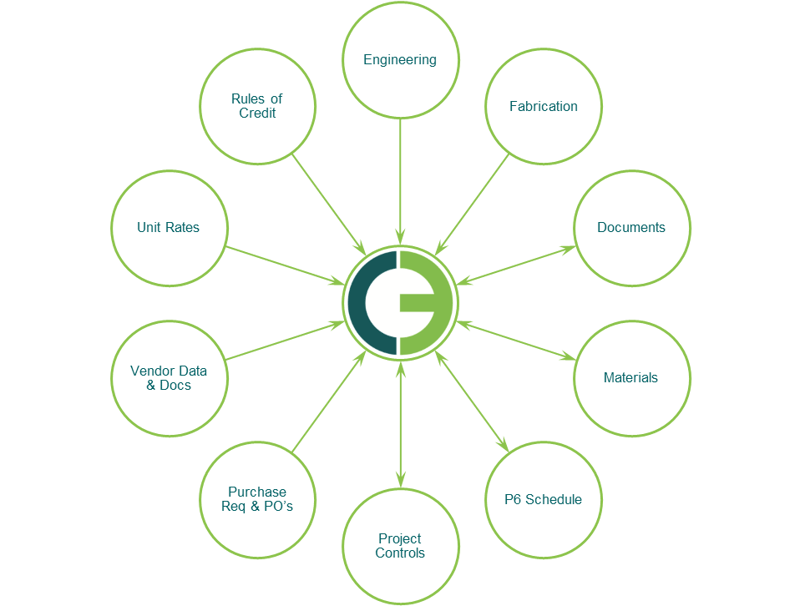
Why API Integrations?
O3’s API integrations always follow strict rules, can be scheduled at any time, and are scalable. API integrations allow the automated process to deliver huge value to users. Since O3 has API access to import anything automatically that can be imported manually, the process to move to automated interfacing is a no-brainer.
When humans are managing this you can count on human errors. That means more time tracking down and fixing the errors. It also means no strict rules have to be followed.
But with the help of APIs, you can count on rules to sort out any errors. Automating the interface process also allows them to be scheduled during off-hours which allow the work package to be updated in real-time.
On one of our projects, we’ve saved an estimated 70 hours a week. This was done on over 50 data connection points on just one project.
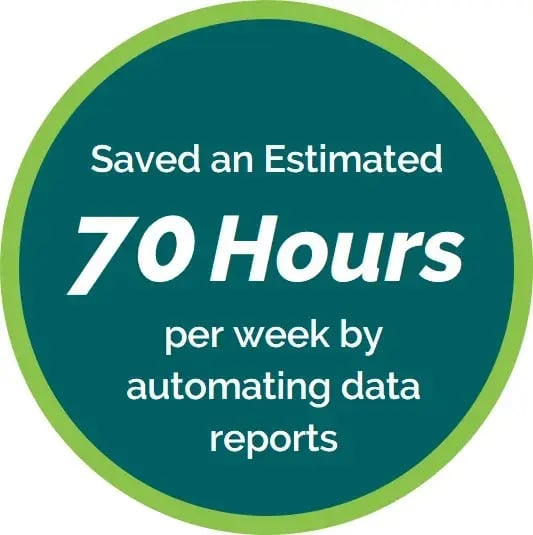
O3 makes all of this happen by following best practices. We continue to cycle through the process and expand. Coordination between the IT department, AWP manager, data experts, and different contractors is required for data discovery. O3 project managers continue to meet regularly with the AWP team to confirm the decisions being made and to have access to a materials management expert. O3 is constantly meeting with clients to ensure that value is being provided. That data is mapped from the source fields to the destination fields using O3. This is done frequently from daily to weekly to monthly based on need.
The biggest benefit to managing data is that Owners and Executives no longer need to track down relevant information. It’s now available at any time from anywhere. Progress on Engineering Work Packages and drawings will be available for construction without the engineers having to change their processes. WorkFace Planners can watch constraints automatically get created when a material is not available due to Installation Work Package execution. Since O3 has unlimited users, everyone can see the data that you need them to see. Overall communication improves and productivity is more efficient.
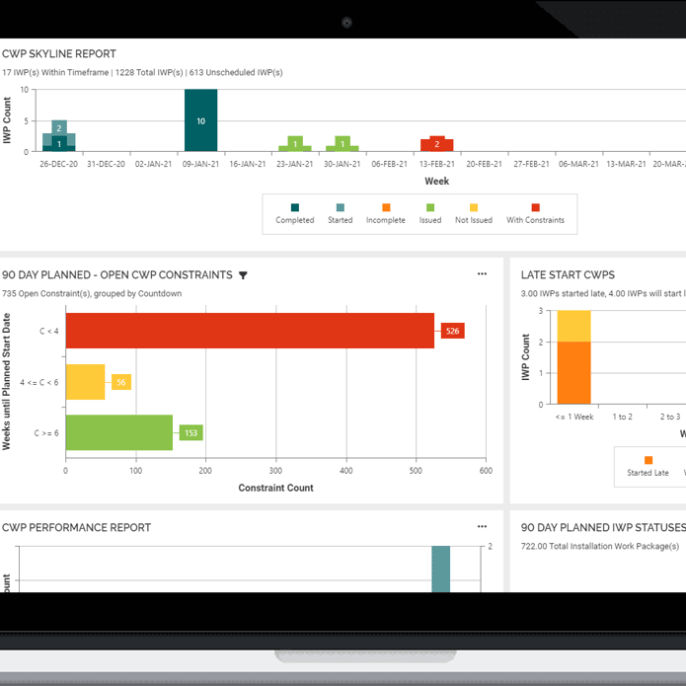